Overview
Piling is a fundamental technique in construction, used to transfer the load of a building deep into the ground to ensure stability and structural integrity. In a city like London – where geology can shift dramatically from one borough to the next – choosing the right piling method is critical for residential, commercial, and infrastructure projects . From house extensions to skyscrapers, piles allow structures to stand safe and level on ground that would otherwise be too weak or unstable. In fact, London’s tallest buildings have historically required extremely deep, large-diameter piles to anchor them in the capital’s soft soils . This expert guide explores the types of piling, the city’s unique soil challenges, and how specialist contractors (like KHB Piling LTD) implement modern, compliant solutions.
📌 What Is Piling?
Piling is a type of deep foundation where long, slender columns (known as piles) are driven or drilled into the earth to support a structure. It’s often employed in areas where near-surface soils cannot safely bear the weight of a building using conventional shallow footings. By transferring loads to deeper, more stable layers, piling provides a secure base for everything from new-build homes to large bridges.
Main functions of piling:
-
Distribute heavy loads to stronger soil or rock layers deep underground, preventing overstressing of weak surface soils.
-
Minimise settlement, ensuring the building doesn’t sink or tilt over time as the ground consolidates.
-
Resist lateral forces (such as wind or ground movement) by fixing the structure firmly into the ground.
-
Enable construction on challenging sites, including those with high water tables or restricted space, where traditional foundations aren’t feasible.
(In summary, piling allows construction on sites that would otherwise be unsuitable by effectively bypassing poor soil and finding firm support at depth.)
🧱 Common Types of Piling in London
London contractors employ a range of piling techniques, each suited to specific ground conditions and project constraints. For example, mini piling rigs – like the one shown below – are compact machines ideal for tight, access-restricted sites. The following are some of the most common piling methods used across the capital:
-
Mini Piling
Mini piling uses small-diameter piles (typically 100–300 mm) and lightweight rigs, making it ideal for sites with limited access or sensitive surroundings. The piles can be steel-cased or augured, and they cause minimal vibration and noise during installation. This method is popular for reinforcing existing structures or building in densely built areas where larger machinery can’t operate.
🔍 Best for:
-
House extensions and conservatories (where working space is limited)
-
Urban infill developments on tight plots
-
Basement conversions in dense residential areas (e.g. Camden or Fulham terraces)
-
-
CFA (Continuous Flight Auger) Piling
CFA rigs use a continuous flight auger to drill a deep hole and fill it with concrete, all in one operation.
In CFA piling, a continuous auger is screwed into the ground to the required depth, then as the auger is withdrawn, concrete is pumped through the hollow stem to fill the hole. This creates a cast-in-place concrete pile without ever leaving an open bore, which minimises ground movement and sloughing. Because the process is virtually continuous, it’s low-vibration and well-suited to built-up environments.
🔍 Best for:
-
Clay-rich soils like London Clay (where CFA piles can form a good bond)
-
Medium to large-scale residential or commercial projects (e.g. new apartment blocks) where higher load capacity is needed
-
-
Rotary Bored Piling
Rotary bored piling uses powerful drilling rigs with interchangeable tools (augers, buckets, chisels) to penetrate hard or mixed ground. These piles can be much larger in diameter (600 mm and above) and extend very deep, making them suitable for heavy structural loads. Once the borehole is drilled, a steel reinforcement cage is often lowered in, and the hole is filled with concrete.
🔍 Best for:
-
Major infrastructure projects (bridges, high-rise buildings) requiring deep foundations
-
Sites with hard strata or boulders that would stop simpler augers (the rotary method can break through obstructions)
-
Variable ground profiles (e.g. near the Thames or in areas like Battersea) where layers of gravel, chalk, or clay might all be encountered
-
-
Underpinning
Underpinning is a retrofitting technique rather than a new-build piling method, but it’s a crucial part of London’s foundation toolkit. Underpinning involves strengthening or deepening an existing foundation – often by excavating beneath sections of it and casting new concrete support, or by installing mini piles and linking them to the foundation. This prevents further movement and transfers the building load to more stable ground below.
🔍 Best for:
-
Stabilising old Victorian and Edwardian houses (common in areas like Islington or Clapham) that have shallow footings and may suffer from subsidence
-
Properties near large trees or with clay soil that heaves (expands and contracts), causing foundation movement
-
Any structure experiencing settlement or cracks, where additional support is needed after construction
-
(Other piling methods exist – such as driven precast piles or screw piles – but the above are the most frequently employed in Greater London’s mix of tight urban sites and varied geology.)
🧪 Soil Conditions in London
One of the biggest challenges for foundation engineering in London is its geological complexity . The capital sits atop a patchwork of soil types – each with different properties – often layered over one another. A thorough geotechnical investigation (borehole drilling, lab tests, etc.) is essential before selecting a piling method, because the strata beneath one neighbourhood can differ greatly from those in another.
The table below highlights a few characteristic London soil types and how piling strategies are typically matched to them :
Soil Type |
Description |
Recommended Piling Method |
---|---|---|
London Clay |
Stiff, high-density clay; prone to shrink–swell with moisture changes (can cause subsidence) |
CFA piling (continuous flight auger) for minimal vibration and good shaft friction |
Bagshot Sands |
Loose, sandy soil; free-draining but not very load-bearing (often found capping the clay on hills) |
Rotary bored piling to reach deeper stable strata below the sand layer |
Gravels & Silts |
Variable river terrace deposits, often water-bearing (high water table) and non-cohesive |
Site-specific mix – often rotary or CFA piles with casing, plus de-watering as needed |
Made Ground |
Man-made fill (rubble, old brick, etc.); unpredictable composition and strength |
Mini piling or CFA piling (flexible methods that can handle obstructions and reduce disturbance) |
Key point: Every project in London should start with a soil survey. Understanding whether you’re dealing with shrinkable clay, loose sands, or reclaimed ground is vital. Engineers will design the pile type, diameter, depth, and spacing based on soil data to ensure safety and cost-efficiency. Notably, London Clay’s tendency to dry out and swell again can lead to structural issues near the surface – which is why deeper pile foundations are so common in the city. By tailoring the foundation to the ground conditions (for example, using CFA piles in clay versus drilled piles in sand) , contractors can avoid problems and optimise performance.
🛠️ Key Considerations When Planning Piling in London
When planning a piling project in London, there are several important factors and local requirements to keep in mind:
-
Access Limitations: Many sites in Central London or dense residential areas have restricted access and low working room. This impacts the choice of equipment – compact piling rigs or sectional rigs may be needed where a large machine can’t fit. Additionally, built-up areas often demand low-noise, low-vibration methods to avoid disturbing neighbours or destabilising adjacent structures. Early planning for logistics (road closures, crane locations, delivery of materials) is essential in tight urban sites.
-
Environmental Compliance: All foundation work must comply with UK standards and building regulations. This includes adhering to BS EN 1997 (Eurocode 7) for geotechnical design and meeting the requirements of Building Regulations Part A (Structure). Piling contractors should follow the latest codes of practice (e.g. BS 8004 for foundations) to ensure safety and quality. Environmental rules also cover noise, vibration, and disposal of spoil – in London, councils often set limits on construction noise and working hours. Every project should have a method statement demonstrating that the piling technique chosen will meet these standards.
-
Third-Party Agreements: Building close to other properties means you must consider your neighbours. Most London piling jobs near a boundary will require compliance with the Party Wall etc. Act 1996, which involves serving formal party wall notices and sometimes negotiating neighbourly agreements before work starts. These legal agreements ensure that any potential movement or damage to adjacent buildings is monitored and rectified. Early communication with neighbouring owners and obtaining the necessary permissions (party wall awards) can prevent disputes and delays. For larger projects, liaising with local authorities and utility companies (to avoid hitting underground services) is also crucial.
-
Site Investigations: As noted above, a geotechnical investigation is the foundation of a successful piling scheme. Soil tests (such as boreholes, Standard Penetration Tests, lab analyses of clay/sand properties) should be conducted to profile the ground . A Ground Investigation Report (GIR) or at least preliminary borehole logs are often required by building control before approval is given to the foundation design . These investigations identify the bearing capacity of the soil, the depth of any strong layer, and potential hazards (like high groundwater or buried obstructions). Skipping this step is risky – without proper soil data, piles could be under-designed or over-designed. In London, site investigation is not just good practice but effectively mandatory for compliance , ensuring that the piling solution is safe and appropriate for the ground conditions.
(In summary: tight access, strict regulations, neighbour considerations, and thorough ground surveys are the four pillars of planning a piling project in London. Addressing each of these early will lead to a smoother construction process.)
🌱 2025 Trends in Piling & Foundation Engineering
Like all construction fields, foundation engineering continues to evolve. In 2025, several trends and innovations are shaping how piling is done in London and beyond:
-
Low-Carbon Materials: There’s a big push to reduce the carbon footprint of construction. Piling contractors are exploring green alternatives such as using recycled steel for reinforcement and low-cement or geopolymer concrete mixes for piles. These materials cut down on CO₂ emissions without sacrificing strength.
-
AI-Driven Site Monitoring: On busy urban sites, ensuring safety and performance is paramount. Modern projects now use smart sensors and AI monitoring systems for real-time analysis of pile driving – detecting any unusual vibrations, tracking how each pile settles under load, and providing instant feedback to engineers . This technology helps prevent issues by catching them early, and it optimises the installation process (for example, adjusting drilling if one area shows unexpected resistance).
-
Digital Twin & BIM Integration: Piling is becoming more data-driven. Engineers create digital twins of foundation systems – detailed 3D models in Building Information Modelling (BIM) software – to simulate how piles will behave and to plan the construction sequence virtually. This integration means that the piling plan is coordinated with the overall building model, reducing clashes and allowing for precise positioning. It also helps with asset management, as the completed piles (and their test data) become part of the building’s digital record.
-
Zero-Vibration Piling Systems: To address the ever-stricter noise and vibration limits in London (especially near sensitive structures like historic buildings or hospitals), new silent piling techniques are being adopted. These include hydraulic press-in piling rigs (such as the Giken system) that literally press piles into the ground without hammering , and other vibrationless methods like rotary drilling with full-length casing. Such systems operate with minimal disturbance – some can even be used at night in residential areas due to their low noise output. While slower than traditional driven piles, zero-vibration methods are increasingly in demand for environmentally sensitive projects.
(By staying abreast of these trends – sustainability, automation, digital planning, and noise reduction – leading contractors ensure their methods remain state-of-the-art and compliant with what both regulators and clients expect in 2025.)
🧠 Why Expert Contractors Matter
Piling is literally the foundation of your project’s success – there is very little room for error. That’s why hiring a reliable, experienced piling contractor (such as KHB Piling LTD) is so important. Expert contractors bring specialized knowledge and equipment to navigate London’s challenges. They will ensure that:
-
All regulations are met: Professional contractors keep your project in line with building codes and standards, obtaining the necessary approvals and certifications. This avoids legal issues and ensures safety from the outset.
-
Risks are minimised: Soil-related risks like heave, excessive settlement, or even foundation collapse are proactively managed. Through proper design and installation techniques, an expert will greatly reduce the chance of structural problems down the line.
-
Budget and timeline stay on track: With their experience, specialist contractors can accurately estimate what’s needed and prevent costly surprises. They design the piling scheme efficiently – avoiding over-engineering – and execute it swiftly with the right machinery. This means you won’t face expensive delays or have to redo work due to mistakes.
In short, an expert piling firm provides peace of mind that your building will stand on solid support. KHB Piling LTD, for example, has successfully delivered 500+ projects across London – from complex basement excavations in Chelsea to new-build developments in Twickenham – honing their techniques on all ground types and site conditions. Their expertise ensures your foundation is done right the first time, saving you time, money, and headaches.
📍 Areas We Serve in Greater London
(KHB Piling LTD proudly serves clients across the Greater London area, including but not limited to:)
-
Central London: Westminster, Kensington, Chelsea, City of London, and surrounding districts.
-
North London: Barnet, Finchley, Enfield, Haringey, and more.
-
South London: Clapham, Dulwich, Streatham, Tooting, Wimbledon, etc.
-
West London: Chiswick, Ealing, Richmond, Hammersmith, Fulham, etc.
-
East London: Hackney, Greenwich, Barking, Ilford, and Docklands areas.
(Whether your project is in a dense urban block or a suburban neighborhood, we have the local knowledge and equipment to handle the ground conditions there.)
📊 Frequently Asked Questions (FAQ)
What’s the typical cost of piling in London?
Piling costs can vary widely, but as a rough guide: £120–£250 per linear metre of pile is common, depending on the pile type, diameter, depth, access limitations, and ground conditions. For example, smaller-diameter mini piles are on the lower end of the cost range, whereas large-diameter bored piles in hard ground or complex setups cost more. (Always get a detailed quote, as each site will differ.)
How long does piling take?
It depends on the project size and method. For a small job like a house extension with a half-dozen mini piles, the installation might be 3–5 days on site. Larger commercial projects (say a new multi-storey building with tens of piles) could take 2–4 weeks to complete the piling phase. These estimates include setting up the rig, drilling or driving the piles, and any testing. Modern techniques are quite efficient – often an individual pile can be drilled and concreted in just an hour or two, but overall schedule depends on the number of piles and working conditions.
What’s the difference between mini piling and CFA piling?
Mini piling refers to the use of relatively small, light piles (and equipment) – it’s perfect for sites with restricted access or low headroom, and it generally causes less noise/vibration. However, mini piles are typically narrower and may not carry as much load with a single pile. CFA (Continuous Flight Auger) piling involves larger diameter piles installed by drilling out soil with an auger and pumping in concrete. CFA piles are great for achieving higher load capacity, especially in cohesive soils like clay, and you can install them with very little vibration. In short: mini piling is a smaller-scale, more flexible solution for tight spaces or light loads, whereas CFA piling is a heavy-duty solution for bigger projects and clay sites.
Is a site survey or soil test really necessary before piling?
Absolutely yes – you should never skip a proper site investigation when piles are involved. Piling design is entirely dependent on ground conditions; without soil data (from boreholes or test pits), any design would be guesswork. In fact, UK building regulations and local authorities require evidence of geotechnical investigation for foundation works . A soil survey will tell the engineers how deep and what type of pile is needed, and it might reveal issues (like high water table or soft layers) that influence the construction method. If you don’t do a survey, you risk either building a foundation that fails (if the ground is weaker than assumed) or wasting money on an over-engineered solution. Bottom line: a modest upfront investment in a ground investigation can save huge costs and troubles later on.
🏆 Recommended Resources
-
British Standards Institution (BSI) – BS EN 1997-1 (Eurocode 7: Geotechnical Design) and BS 8004 (Foundations Code of Practice) for detailed technical guidelines.
-
Federation of Piling Specialists (FPS) – Industry body with best practice guides and a directory of accredited piling contractors.
-
Building Control Portal – GOV.UK – Official government resource on building regulations (including structural requirements in Part A and guidance on foundations).
(These resources offer further reading for those interested in the technical and regulatory framework around piling in the UK.)
📞 Get a Free Site Consultation Today
Need a piling expert for your project in London? KHB Piling LTD is here to help – from initial surveys to completed foundations. Get in touch for a no-obligation consultation and expert advice tailored to your site.
📞 +44 7821 836407
🌐 www.khbpiling.co.uk
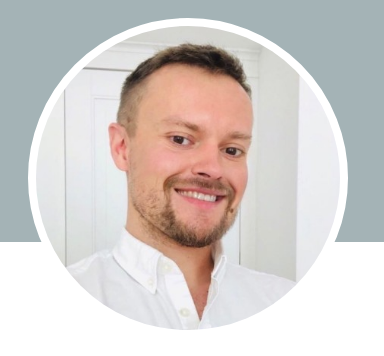
My name is Kamil, and I specialise in piling services in London. I am dedicated to advancing KHB Piling LTD, a trusted contractor delivering high-quality foundation solutions for both residential and commercial projects. With the expertise and commitment of our team, we provide reliable piling services, including mini piling and CFA piling, tailored to meet the unique requirements of each client.